One Unit Dust Collector Together with Fan and Motor
Short Description:
Through the gravitational force of the fan, welding fume dust is sucked into the equipment through the collection pipeline, and enters the filter chamber. A flame arrester is installed at the inlet of the filter chamber, which filters the sparks in the welding fume dust, providing dual protection for the filter cylinder. Welding fume dust flows inside the filter chamber, utilizing gravity and upward airflow to first directly lower the coarse smoke dust into the ash collection drawer. Welding fume containing particulate dust is blocked by a cylindrical filter cylinder, Under the action of screening, particulate dust is trapped on the surface of the filter cartridge. After being filtered and purified by the filter cartridge, welding smoke and exhaust gas flow into the clean room from the center of the filter cartridge. The gas in the clean room is then discharged through the equipment exhaust outlet after passing the standard through the induced draft fan.
Working Principle
Through the gravitational force of the fan, welding fume dust is sucked into the equipment through the collection pipeline, and enters the filter chamber. A flame arrester is installed at the inlet of the filter chamber, which filters the sparks in the welding fume dust, providing dual protection for the filter cylinder. Welding fume dust flows inside the filter chamber, utilizing gravity and upward airflow to first directly lower the coarse smoke dust into the ash collection drawer. Welding fume containing particulate dust is blocked by a cylindrical filter cylinder, Under the action of screening, particulate dust is trapped on the surface of the filter cartridge. After being filtered and purified by the filter cartridge, welding smoke and exhaust gas flow into the clean room from the center of the filter cartridge. The gas in the clean room is then discharged through the equipment exhaust outlet after passing the standard through the induced draft fan.
As the thickness of the dust layer on the surface of the filter cartridge increases, the ability of the filter cartridge to filter and purify air will decrease, and the pressure drop of the inlet and outlet air flow of the equipment will increase, resulting in a decrease in purification efficiency. To avoid significant changes in the filtration pressure of the equipment, the reverse blowing and cleaning system of the equipment operates simultaneously with the filtration system. The pulse control instrument controls the opening of each electromagnetic pulse valve according to the set pulse width and pulse interval sequence. The compressed air in the air bag passes through the pulse valve through the blowing hole on the blowing pipe, ejecting a high-speed and high-pressure jet air flow, causing an induced air flow that is several times the volume of the jet air to enter the filter cartridge, Instantaneous positive pressure occurs inside the filter cartridge, causing the cartridge to expand, causing the dust deposited on the cartridge to deform and fracture, separating in blocks from the cartridge. This sequentially restores the ability of the cartridge to filter and purify air to its initial state, reducing excessive wind resistance pulsation, maintaining a balanced pressure drop and stable filtration efficiency. The dust peeling off the surface of the filter cartridge falls into the ash collection bucket, and the dust in the ash collection bucket can be cleaned regularly according to the working conditions.
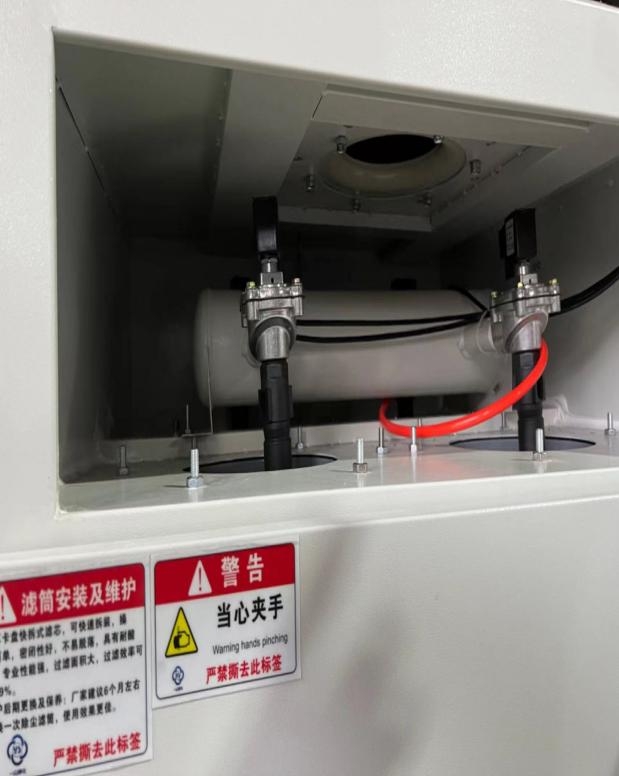
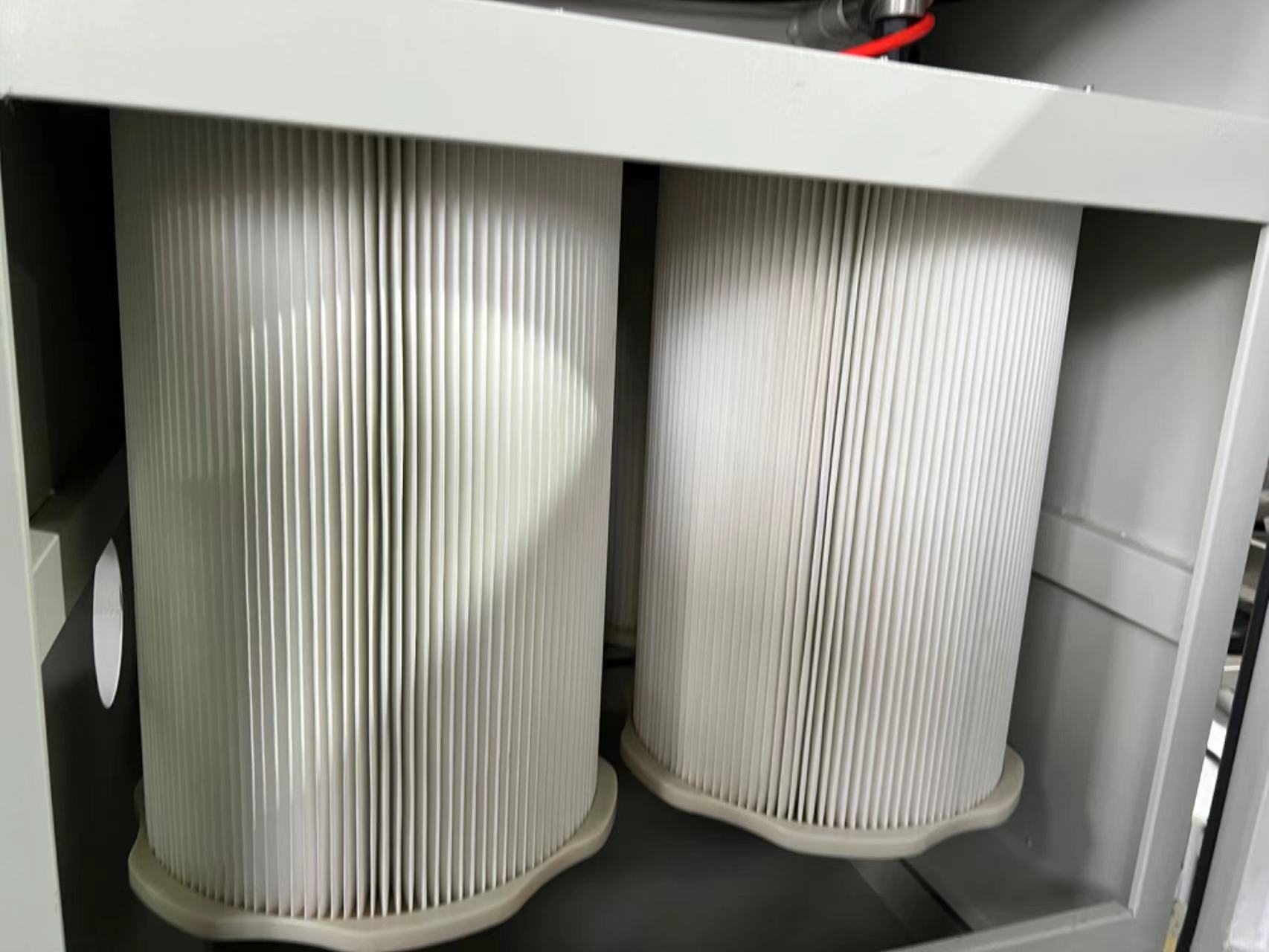
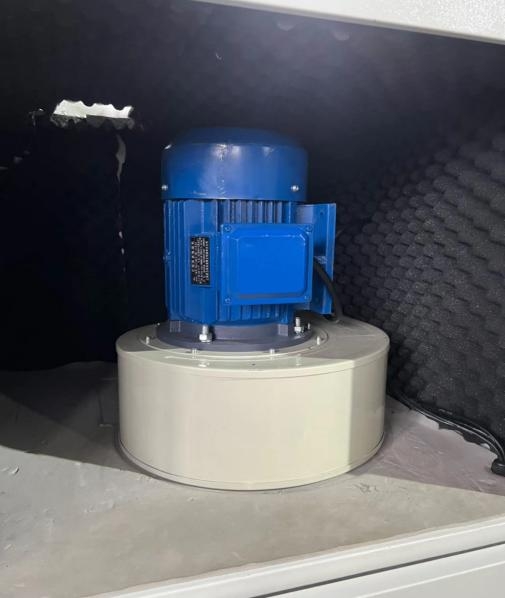
Equipment Features
1. The filter material is an important part of the filter dust collector and the heart of the dust removal equipment. Its performance and quality are crucial for the service life and smoke removal performance of the equipment. The filter cartridges used for the welding smoke and dust purifier produced by our company are all made of imported PTFE polyester fiber material. This material has extremely low friction coefficient, good wear resistance, and excellent chemical stability, high accuracy, and good filtration effect. According to the working conditions, the maximum fineness can reach 0.2 micrometers, and the purification efficiency is 99.99%. The surface of this material is extremely smooth and not easy to adhere, making it easier to pulse back blow clean. The service life of the filter cartridge is extremely long, and can reach 2-3 years under normal operating conditions.
2. A dust baffle is installed at the dust inlet of the high-efficiency filter cartridge dust collector, which has a buffering and wear-resistant effect and will not directly impact the filter cartridge at high speed, thus extending the service life of the filter cartridge.
3. Ash cleaning method: The high-efficiency filter cartridge dust collector adopts pulse jet automatic ash cleaning, which means that the filter cartridges are automatically cleaned in sequence one by one. The pulse valve is opened once to generate a pulse action, and the intensity and frequency of pulse jet can be adjusted. The ash cleaning effect is good, and the cleaning and filtering do not affect each other, ensuring that the equipment is always in good working condition and improving production efficiency.
4. The consumable performance of the high-efficiency filter cartridge dust collector is stable, and replacement is convenient and fast.